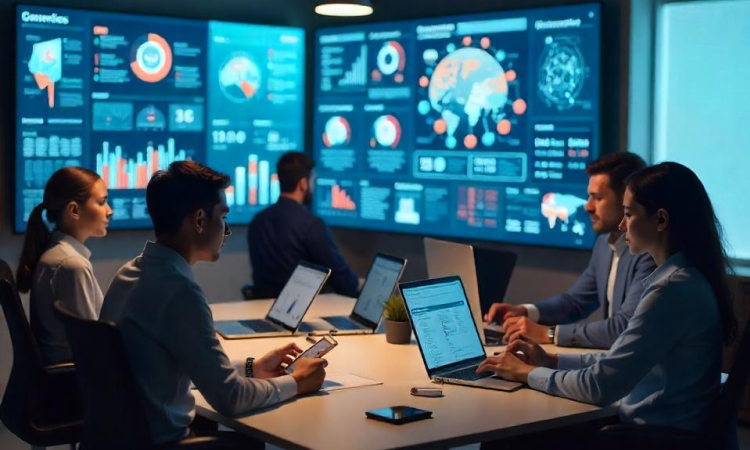
The manufacturing industry is experiencing a digital transformation driven by automation, the Internet of Things (IoT), and Artificial Intelligence (AI). While much of the conversation around AI in manufacturing has focused on improving operational efficiency and enhancing productivity through automation, there’s another critical area that AI is profoundly impacting—workforce engagement.
Manufacturing workers are a core part of any operation, and ensuring their engagement, productivity, and well-being is vital for the success of any organization. Engaged employees are more likely to be productive, loyal, and motivated, which leads to better performance and improved business outcomes. However, manufacturing companies often face challenges related to workforce retention, skill development, and employee satisfaction.
AI, when applied correctly, has the potential to significantly improve workforce engagement in manufacturing environments. By integrating AI-driven tools, manufacturers can foster an environment where employees feel more connected to the work they do, improve their productivity, and align their goals with company success.
In this blog, we’ll explore how AI is transforming workforce engagement in the manufacturing industry, highlighting the key trends, challenges, and practical applications that can lead to a more engaged and productive workforce.
Manufacturers face several unique challenges when it comes to workforce engagement:
AI technologies are helping manufacturers improve workforce engagement by addressing the challenges outlined above. By leveraging AI in areas like workforce management, skill development, safety, feedback systems, and productivity tracking, manufacturers can create a more supportive and empowering environment for their employees.
AI can enhance employee engagement by providing personalized training programs that cater to individual learning needs. AI-powered learning platforms can analyze a worker's skills, knowledge gaps, and learning style to deliver customized training content, making learning more engaging and relevant.
Example: An AI system could monitor an employee’s progress through a training program and recommend specific courses or on-the-job training opportunities that would help them improve or adapt to new technologies.
AI-driven tools can provide real-time feedback to employees, which is crucial for engagement. By monitoring performance and productivity in real-time, AI can offer personalized feedback and even recognize achievements. Automated feedback systems can help employees identify areas for improvement and highlight their strengths.
Example: AI tools integrated into production systems can track key performance indicators (KPIs) like output quality, speed, and safety. When an employee meets or exceeds certain targets, the system can instantly alert supervisors to offer praise or rewards.
Safety is a top concern in manufacturing, and AI plays a key role in monitoring and preventing accidents. By leveraging AI-powered sensors, cameras, and predictive analytics, manufacturers can create safer work environments, which directly impacts employee engagement and satisfaction.
Example: AI-based predictive maintenance systems can detect potential equipment failures before they happen, ensuring that machinery is always functioning properly and minimizing the risk of accidents. AI-powered cameras and sensors can also detect unsafe behaviors (such as not wearing proper protective gear) and alert supervisors immediately.
AI-driven scheduling tools can optimize shift planning based on employee preferences, availability, and workload. When employees have a say in their schedules or when their shifts are organized to prevent burnout, they are more likely to stay engaged with their work. AI systems can also help distribute tasks fairly, avoiding overwork or underutilization of employees.
Example: An AI-powered system could analyze production demands, employee preferences, and even physical capability to create optimized, fair schedules that match the demand while promoting a healthy work-life balance.
AI-driven wellness programs are becoming increasingly popular in manufacturing environments. These programs use AI to monitor worker health and well-being, identify stress factors, and promote healthy behavior. AI tools can track patterns like employee fatigue, work hours, and physical exertion, offering insights that can help improve well-being and engagement.
Example: AI-powered wearable devices can monitor workers’ physical activity levels, detect signs of fatigue, and provide alerts to suggest breaks or proper rest periods. These devices can also collect data to help managers understand how physical strain is affecting workers and make necessary adjustments.
AI tools can facilitate better communication and collaboration between workers, managers, and departments, ensuring that employees feel more connected and involved in decision-making. AI chatbots or virtual assistants can answer common questions, provide company updates, or help employees navigate complex processes.
Example: A virtual assistant powered by AI can help a worker quickly access information about production schedules, machine status, or even employee benefits, improving their productivity and engagement by reducing frustration from lack of information.
Case Study 1: Siemens – AI-Powered Skill Development
Challenge: Siemens wanted to enhance workforce engagement by helping its employees develop the skills needed for the future of manufacturing.
Solution: Siemens implemented an AI-driven learning platform that provided personalized training content based on each employee’s skills and career aspirations. This allowed workers to continuously upgrade their skills and stay engaged with their professional development.
Results: Employees felt more confident and satisfied with their work, leading to higher productivity and lower turnover rates. The platform also helped Siemens improve its talent pipeline by ensuring workers had the skills needed to meet future demands.
Case Study 2: General Electric (GE) – AI for Worker Safety
Challenge: General Electric (GE) sought to improve employee safety and reduce workplace accidents in its manufacturing plants.
Solution: GE deployed AI-powered cameras and sensors to monitor workers and machines for safety hazards. The AI system used computer vision to identify unsafe behaviors or equipment malfunctions, sending real-time alerts to supervisors and workers.
Results: Workplace accidents decreased by 25%, and employees reported higher confidence in the safety measures in place. This led to increased engagement as workers felt their well-being was a priority.
Case Study 3: Toyota – AI for Workforce Scheduling
Challenge: Toyota faced challenges in scheduling workers efficiently across its production lines to meet fluctuating demand.
Solution: Toyota implemented an AI-based scheduling system that analyzed historical data, demand forecasts, and worker preferences to create optimized schedules. The system also considered employee fatigue levels and work-life balance.
Results: Worker satisfaction increased by 20%, and absenteeism rates dropped as employees were happier with their schedules. The system also improved overall operational efficiency, ensuring that the right number of workers were available at peak times.
AI is transforming workforce engagement in the manufacturing industry by addressing the key challenges faced by workers and employers. By leveraging AI to enhance training, provide real-time feedback, improve safety, optimize scheduling, and promote well-being, manufacturers can create a more engaged, productive, and satisfied workforce. As AI continues to evolve, the potential for enhancing workforce engagement will only grow, leading to better retention rates, increased job satisfaction, and improved overall business outcomes for manufacturers.
we’re committed to providing cutting-edge AI solutions that empower businesses to thrive in a fast-evolving digital landscape. Subscribe to our newsletter and stay informed on the latest advancements, industry insights, and how we can help transform your business with AI.